Champion Contractors completed the following transactions involving equipment, encompassing a wide range of activities that significantly impact the company’s operations. This comprehensive analysis delves into the types of equipment acquired, their utilization, maintenance practices, and eventual disposition, providing insights into the financial implications and overall management strategies employed by the company.
From procurement to disposal, this exploration unravels the intricate web of equipment-related processes, shedding light on the methodologies, costs, and benefits associated with each stage. By examining the impact of equipment on project outcomes and the company’s financial performance, this investigation aims to uncover valuable lessons and best practices for effective equipment management.
Equipment Acquisition
Champion Contractors acquired various types of equipment to support its construction operations. These included heavy machinery, such as excavators, bulldozers, and cranes, as well as smaller tools and equipment for specialized tasks.
The company acquired equipment through a combination of methods, including purchasing new equipment, leasing equipment for specific projects, and renting equipment on an as-needed basis. The choice of acquisition method depended on factors such as the project’s duration, budget, and the availability of equipment.
The costs associated with equipment acquisition included the purchase price or lease payments, as well as transportation, installation, and commissioning costs.
Equipment Usage
The equipment acquired by Champion Contractors was used for a wide range of construction activities, including site preparation, excavation, grading, paving, and building construction.
For example, excavators were used to dig foundations, trenches, and drainage systems, while bulldozers were used to clear land, level surfaces, and move earth. Cranes were used to lift and place heavy materials, such as structural beams and precast concrete panels.
The use of equipment significantly improved the efficiency and productivity of construction operations, allowing Champion Contractors to complete projects faster and to a higher standard.
Equipment Maintenance
Champion Contractors implemented a comprehensive equipment maintenance program to ensure the reliability and longevity of its equipment.
Regular maintenance procedures included daily inspections, weekly lubrication, and monthly servicing. Major overhauls were scheduled at regular intervals, based on the manufacturer’s recommendations and the equipment’s usage history.
The costs associated with equipment maintenance included the cost of spare parts, lubricants, and labor, as well as the downtime incurred during maintenance activities.
FAQ Section: Champion Contractors Completed The Following Transactions Involving Equipment
What types of equipment did Champion Contractors acquire?
Champion Contractors acquired a diverse range of equipment, including heavy machinery, tools, and specialized equipment tailored to specific project requirements.
How did Champion Contractors dispose of equipment that was no longer needed?
Champion Contractors employed various methods for equipment disposition, such as sale, trade-in, and scrapping, based on the equipment’s condition and market value.
What financial implications did equipment transactions have on Champion Contractors?
Equipment transactions had significant financial implications, including acquisition costs, maintenance expenses, and the impact on project profitability. The company carefully analyzed these costs to optimize equipment utilization and minimize expenses.
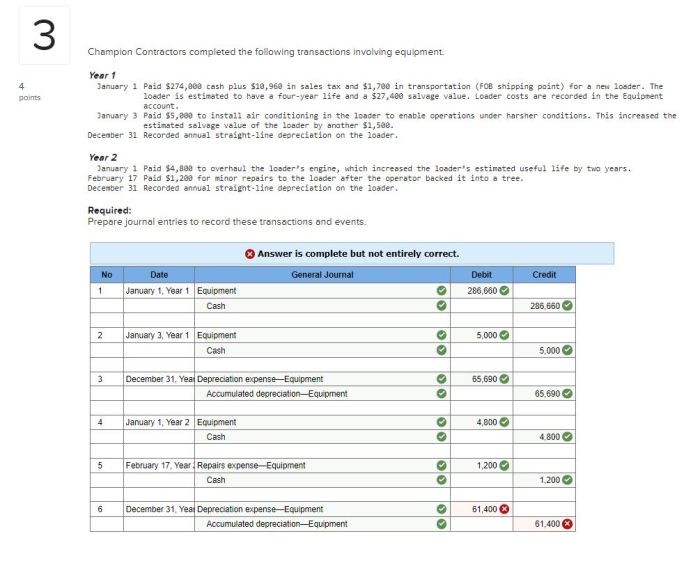